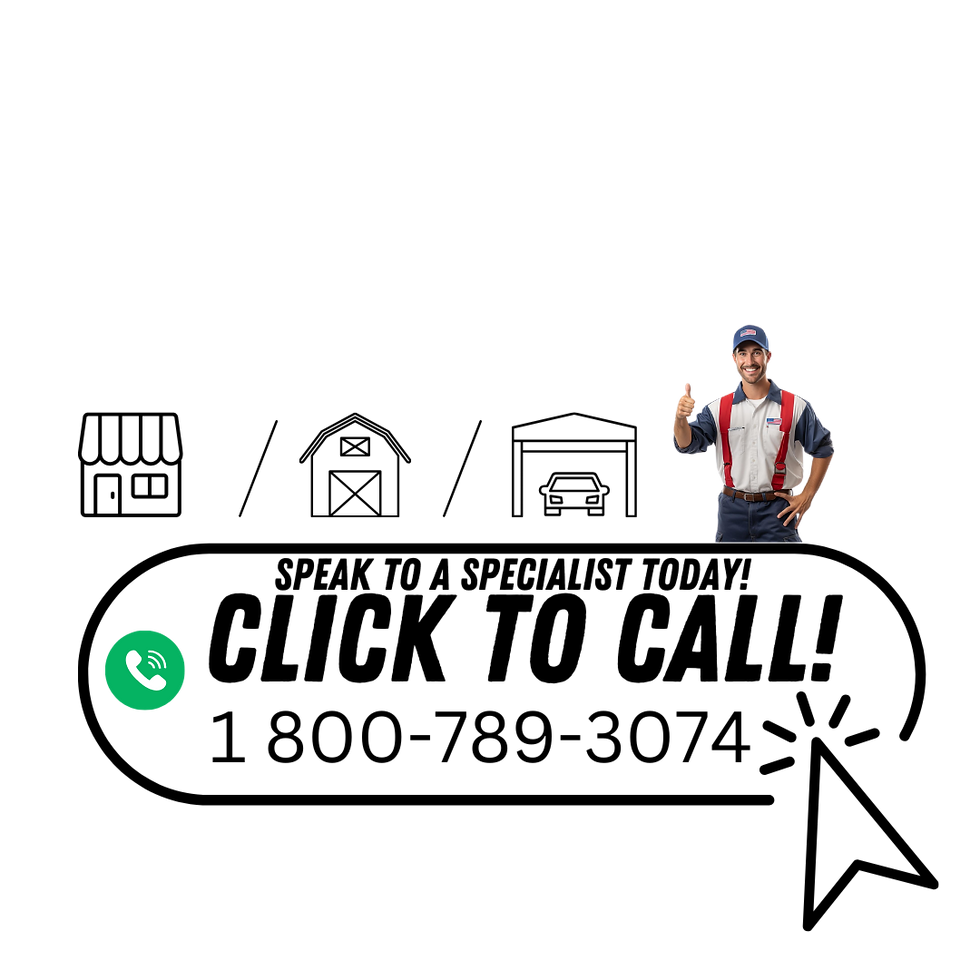
Thinking About Getting A Custom Metal Building For Your Property? In This Guide, We Answer All The Pressing Questions That You Have, And A Few You Don't!
The global prefabricated buildings market is expected to reach $29.65 billion by 2026. This increase across a wide range of industries is due to the many advantages of such buildings.
If you’re interested in a custom metal building, there are a lot of factors to take into consideration before investing.
To find out more, keep reading.
Why Choose A Custom Metal Building?
Custom metal buildings vary a lot in terms of size and design. When looking at investing in one, the final design will depend on what you intend to use it for.
Some of the most common uses include:
Storage sheds
Barns
Garages
Workshops
Warehouses
Factories
Agricultural storage
The list goes on, and ultimately, custom metal buildings can serve any purpose you want them for.
Advantages Of Custom Metal Buildings
What investing in a new building, you have a number of options in terms of construction materials and methods. Custom metal buildings are becoming more popular due to having several advantages over other types.
Strength and Durability
Steel is one of the most common structural materials in the world. It has several useful qualities, but perhaps the most prominent is its strength and durability.
Older buildings made for similar purposes were traditionally made from wood. It is plentiful and easy to use. In modern times, however, steel has become very easy to manufacture, making it a far better choice.
High-quality steel is incredibly strong, capable of standing up to natural forces, such as heavy wind and rain, which could damage weaker structures.
On top of this, wood is far more susceptible to rot, insect infestation, and gradual wear. Steel itself can be susceptible to corrosion, but our sheds at The NC Builders are made from galvanized steel to avoid this.
The galvanization process covers the steel in a layer of zinc, which protects the steel below from any substances that may cause rust or corrosion. This makes our custom metal buildings perfect for use outside.
Cost
As we’ve said, wood could be another potential building material, but despite what you may think, most of the time wood is the more expensive choice.
Steel is cheaper than wood (per square foot). On top of this, the increased durability means a steel structure requires less maintenance and repairs in the long run.
In most climates, thermal insulation is essential. There are several options when it comes to metal building insulations. Two of the primary choices are:
Thin, foil-backed, vapor barrier insulation
Spray foam insulation
Of these two we recommend spray foam as it is the most efficient. While insulation may give a greater initial cost, it can result in significant savings down the line in terms of heating and cooling.
Flexibility
Prefab steel buildings can contain few, or even zero interior columns. This presents tons of options when it comes to the interior layout.
If you intend to store any large equipment in your building, the last thing you want is columns or other structural components to get in the way.
Large rolling or overhead doors also help in this aspect – they make it easier to get large equipment in and out of your building.
Assembly
Depending on the specifications of your building, construction can be incredibly quick. All parts are pre-fabricated and then brought out to your site to make assembly as easy as possible.
Customizability
Wooden structures are also far more difficult to customize, so it is often far easier to make a building to precise specifications when using steel.
Whether your building is being used as a garage, workshop, office, and so on. it can be custom designed to fit that purpose perfectly.
You can choose the length, width, and height of the building, the size, and type of doors, whether there are separations inside or it is an uninterrupted space; all the choices are down to you.
Custom Metal Building Tips
There are a lot of things to think about when investing in a custom metal shed. You want to get the most out of it, and that it is fit for purpose.
The NC Builders can go a long way to make sure your shed comes out exactly how you want it. Below are some tips on certain aspects to consider for your metal shed.
Size
After people buy their first metal building, it is very common for them to regret not going for a larger size.
You should make sure you take the time to get measurements of all equipment, machines, and anything else that needs to be inside. Also, take into consideration any space around this equipment. Walkways, area to work, tool storage, etc.
Before installation, it is also important to make sure there is space around the building site. Installers will need space to move and work to make sure the installation goes smoothly.
On arrival, our installers will usually be in a one-ton truck with a 30′ trailer. They will need space to turn around and access the site on the day.
The NC Builders don’t have set sizes for metal buildings – we will custom make them to whatever size you need. The width can be anywhere from 12′ to 60′, and we have no limit on the building length!
Just note that for steel buildings, the square footage matches the exterior, rather than the interior dimensions. As such, the architectural plan for the exterior will have a larger area than the interior.
Height
Like the square footage, the height of your metal building can match your specific needs. Most metal buildings have a height of around 12′ to 20′, but they can be taller if required.
The height is not measured to the top of the peak, but rather from the floor to the top of the eave.
The number of floors will affect the height, and most metal buildings are either one or two stories tall.
When deciding the height of your building, certain things need to be taken into account. You should look at the height of your equipment, but then consider if you will need to raise it for any reason.
If a machine needs repairs, for example, will a part of it require an extra 5 feet of clearance? Or if your building is being used for storage of a product, will you need to accommodate for future business growth?
Essentially, you need to think about how the building will be used from the start, as well as in the future. You will want to account for any situations or issues that may arise along the line.
Windows and Lighting
Lighting is essential for any metal building, metal or otherwise. The amount of lighting needed depends on your building’s uses.
A very effective way of lighting your building and saving on energy costs is with the use of skylights.
Windows can also be a great source of natural light, and if insulated properly, they can help reduce the costs of both lighting and heating. Being able to open windows for extra ventilation can also be very useful.
Beyond this, you can add additional lighting fixtures as needed to ensure there is always an adequate amount of light.
Doors
Different types of doors are available for different purposes.
Overhead doors will be essential if you plan to move any large equipment in or out, and the clearance will need to be taken into account. If your building store any vehicles, roller doors are ideal.
Normal entrance and exit doors can be installed anywhere for added convenience.
One essential requirement will be emergency exits. In general, a workplace must have at least two possible exits if people need to evacuate.
Other doors you have installed are based on what you want, but in terms of emergency exits, you need to ensure your building is up to code. This will depend on the size and layout of your building, as well as the number of occupants at any given time.
Foundation
Before our installers arrive, your base must meet two requirements.
Firstly, the slab/foundation must meet the sizing regulated by your local authority. This can vary by location, but we recommend a minimum of 6″ perimeter footing around the building perimeter.
Secondly, the foundation needs to be level to properly construct your building. Having this taken care of will make installation of your building quick and easy.
Flooring
When deciding on the flooring of your building, it is important to think about not just how it will look, but also how it will function.
Your building will be on a concrete foundation, but you will more than likely want some sort of finish or covering.
Finished Concrete
Finished concrete can give great aesthetic qualities. There are several possible methods, such as staining, dyeing, etching, or glazing. The final look can mimic many materials to give any look or style you choose.
Waterproof Vinyl
Waterproof vinyl is a cost-effective method that can mimic wood or tile. It will not be affected by water and humidity, and if water does manage to get below the floor, individual planks can easily be lifted.
Epoxy Coating
Epoxy coating is not only aesthetically pleasing but incredibly durable. Using an epoxy coating can help extend the life of your flooring by 10-20 years!
It provides a protective layer that is resistant to impact damage, as well as chemicals. This is especially useful in an environment with tools or volatile materials.
On top of this, it is stain resistant, and can easily be cleaned with just a hose.
Climate
Depending on where your building is, it may have to contend with the elements. This is an especially important factor if your building will be located in an area that is prone to natural disasters.
Events such as hurricanes and earthquakes can be devastating, so if they may occur, the structure must be designed to withstand them as best as possible.
In an area with wildfire risks, there may be certain health and safety regulations to be adhered to.
The ground must be properly leveled and stable in wetlands, or on any land with an elevation change. Drainage may take some extra work here too to ensure it is sufficient.
If there is a significant amount of heavy rainfall, it might be a good idea to add an extra layer of coating to ensure proper protection.
Color
For come, the color of a custom metal building is the first firm choice made in the whole design. You may want your building to match your company’s branding or logo, or maybe you want it to match other buildings in the area.
If this is your first building, you may still need to make up your mind. If you’re unsure, there are a few things you can think about to help you decide.
The nature of your business, or even your customer demographics, may come into play. If you are catering to older, more reserved customers, a subtle color scheme may be ideal. A younger audience may prefer brighter, bolder colors.
The location can also be a factor. Is it surrounded by other buildings? Do you want it to fit in? Or stand out?
Thinking about the future is important here too – is it likely that your choice of color may go out of style quickly? It may be safer to go with a color scheme that you think will stand the test of time.
Cost
It’s a very important question – what does a custom metal building cost?
This is a very difficult question. It is safe to say that pre-fab buildings naturally help here, as waste material is kept to a minimum, as well as the amount of labor required for assembly.
Remember though, all of the factors above come into play when determining how much your building may be. Keep in mind that there are many ways that you can keep the cost down.
All the factors mentioned above come into play here. If all of these options are properly taken into account, they can provide huge savings.
The NC Builders also offer multiple affordable payment options for almost all credit types.
How To Make Your Choice
There is a lot to think about when purchasing a custom metal building. It can be a long and complicated process.
The team at The NC Builders has plenty of knowledge and experience, so don’t hesitate to contact us and let us know what you need.
Whether you already have a design in mind, or you just have some questions about custom metal buildings, we are always happy to help!
Comentários